Arcam Unveils Metal 3D Printers

A view inside of an Arcam 3D metal printer’s electronic beam build area. Image courtesy of Arcam AB.
Latest News
July 6, 2016
Arcam AB has two new EBM (electron beam melting) metal 3D printers, the Arcam Q10plus and the Arcam Q20plus. With the new printers, Arcam introduces Arcam xQam, an X-ray based technology for high-precision auto-calibration and improved beam control as well as an all-new software platform called EBM Control 5.0.
Arcam’s EBM process uses an electron beam to melt metal powders layer-by-layer to fabricate fully dense metal components. The process takes place in a controlled vacuum that ensures a clean build environment and helps maintain the chemical specification of the build material.
Arcam’s MultiBeam deflection lens technology allows its 3D printers to maintain several melt pools simultaneously. This melting strategy, explains Arcam, enables optimization of surface finish, precision and build speed simultaneously. The resulting components are free from residual stress and have material properties better than cast and comparable to wrought materials, according to the company.

Both the Arcam Q10plus and the Arcam Q20plus have interior build chambers designed for easy powder handling, a camera-based monitoring system for inline part quality verification and Arcam xQam technology for high-precision auto-calibration. The 3D printers come with EBM Control 5.0 software that, says Arcam, adds functionality for more efficient and accurate beam control compared to its predecessor as well as new melt strategies that can improve build speed and precision.
Arcam says that its new Arcam Q10plus, which replaces its earlier Arcam Q10 system, is designed for cost-efficient production of orthopedic implants. The company describes the Arcam Q10plus as particularly suitable for the production of high-volume press-fit implants with advanced Tribecular Structures of engineered porous materials as well as one-off custom implants built with data derived from CT scans of individual patients. Its maximum build size is 7.88x7.88x7 in. (WxDxH; 200x200x180 mm). The Arcam Q10plus’ build area, the company adds, allows for optimal stacking of most common implant types.
Arcam says that it designed the Arcam Q20plus for cost-efficient production of aerospace components such as turbine blades and structural airframe components. Based on the Arcam Q10 technology platform, the Arcam Q20plus also includes the inline part quality verification and auto-calibration technologies. However, its bigger 13.77x14.96 in. (350×380 mm) build envelope allows for fabricating larger components as well as stacking of smaller ones. Arcam reports that the Arcam Q20plus can offer up to 15% higher productivity compared to the earlier Q20 machine platform.

Standard materials offered by Arcam include Cobalt-Chrome ASTM F75, Inconel 718 and three types of Titanium – Ti6Al4V, Ti6Al4V ELI and Titanium Grade 2. Additionally, Arcam says it allows and supports customers to independently develop the process for other materials. Arcam’s metal powder supply chain is validated with full traceability for each batch.
Both the Arcam Q20plus and the Arcam Q10plus are delivered with a powder recovery system. Other shared features include an easy-to-use operator interface and software adapted to volume production.
For details on the Arcam Q10plus, click here.
For details on the Arcam Q20plus, click here.
Learn more about Arcam’s metal powders.
Download a brochure describing Arcam’s technology and product line-up.
See why DE‘s editors selected the Arcam Q10plus and the Arcam Q20plus as their Pick of the Week.
Sources: Press materials received from the company and additional information gleaned from the company’s website.
Subscribe to our FREE magazine,
FREE email newsletters or both!Latest News
About the Author

Anthony J. Lockwood is Digital Engineering’s founding editor. He is now retired. Contact him via [email protected].
Follow DE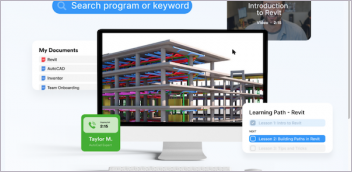

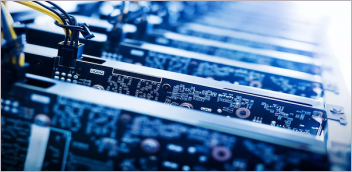
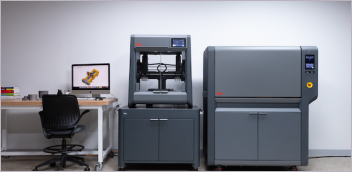