ANSYS Focuses Upfront Simulation at Delphi
A corporate initiative at Delphi Electronics aims to bring benefits of early product simulation to sites around the world.
Latest News
May 1, 2010
By Fereydoon Dadkhah
Most high-technology companies now realize the potential benefits of simulating the performance of their products using tools such as finite element analysis (FEA). They also clearly know that performing analysis early in the design cycle has the potential to identify and solve design problems much more efficiently and cost effectively than later.
![]() This chart shows the hours of ANSYS DesignSpace use at various Delphi sites internationally. |
One company using upfront analysis throughout the product engineering organization is Delphi Electronics and Safety Systems—a division of Delphi Corporation specializing in mobile electronics and transportation systems for the automotive and consumer product industries. Beginning in the late 1990s, Delphi Electronics and Safety embarked on a program to take full advantage of FEA in the product development process. Along with other companies, Delphi Electronics and Safety had been using FEA in a more limited way as a troubleshooting tool often late in a project’s development. The new initiative intended to use FEA as an integral part of the product development process—especially focusing on the use of simulation upfront in the design cycle. To achieve this goal, Delphi started training design engineers in the use of FEA in the early stages of the design process. This program began by classifying engineers according to their skill levels in the use of FEA and in their ability to interpret analysis results. Gradually, the program incorporated use of FEA into the Delphi Electronics and Safety product development plan.
![]() First mode of vibration for bracket that supports an airbag control unit. |
Safeguards such as peer reviews, engineering fundamentals training, and mentoring were implemented to ensure proper use of FEA. Furthermore, Delphi Electronics and Safety has restricted use of this technology to engineers and scientists with a minimum of a bachelor’s degree. Training in the use of the structural mechanics simulation software—in this case, ANSYS DesignSpace on the ANSYS Workbench platform—is a prerequisite at Delphi Electronics and Safety.
Steady-State Thermal Analysis
The most common use of the ANSYS Workbench tool at Delphi is by design engineers engaged in product development. Analysis types include steady-state thermal, free vibration, and linear static stress analysis. More advanced types of analysis, including those involving material or geometric nonlinearity, transient loading, fluid flow, and multiphysics, are performed by full-time analysts. Delphi produces a number of products including those for use in the automotive and consumer product sectors that must meet stringent thermal requirements. A steady-state thermal analysis is, in many cases, the first step in ensuring that the final product will meet the thermal requirements of the customer. Based on usage data collected annually, the ANSYS DesignSpace tool is widely used to perform this type of analysis.
For example, an integrated circuit package used in a transmission controller unit developed by Delphi might undergo a steady-state thermal analysis. Once the steady-state performance is established, transient and system-level analyses are performed to completely characterize the system.
|
In another example, ANSYS DesignSpace software is often used for determination of the natural modes of vibration of a system. When Delphi develops an automotive part, the first step is to ensure that the first few modes of vibration of the product are beyond the minimum values that can be excited by the vehicle’s operation. The image above (right) illustrates a study for the first mode of vibration for a bracket used to support an airbag control unit. Using the ANSYS DesignSpace tool to perform modal analysis, product engineers are able to determine if any changes to the initial design are needed to improve the vibration characteristics of the system. The design then proceeds to the next stage, in which harmonic and power spectral density analyses are performed and any required changes are made.
Upfront Simulation Required
Today, the company has incorporated the use of structural mechanics simulation into the Delphi Product Development Process (PDP) as a requirement. The PDP begins with the concept stage and proceeds to the validation stage when prototypes are built and tested, and finally the program is handed off to manufacturing. This has led to developing much more robust and reliable products as well as greatly reducing or eliminating validation failures. This process is enforced by a Design Failure Modes and Effects Analysis (DFMEA) plan represented by a spreadsheet of possible failure modes for a product and indicating the required analyses to show that the product is immune to specific failures. A large number of engineers in the global Delphi organization use these tools, including the full suite of software in the ANSYS Workbench interface, to perform thermal, stress, vibration, and other general analysis in the course of product development. In 2007, the number of ANSYS DesignSpace users at Delphi exceeded 200, and approximately 30 percent were Delphi Electronics and Safety engineers. Delphi Electronics and Safety users globally logged 11,151 hours on the software, or 34 percent of the total for all sites internationally.
More Info:
ANSYS, INC.
Delphi Electronics & Safety Systems
Fereydoon Dadkhah is the senior engineer of Mechanical Analysis and Simulation at Delphi Electronics and Safety Systems. Send comments about this article to [email protected].
Subscribe to our FREE magazine,
FREE email newsletters or both!Latest News
About the Author

DE’s editors contribute news and new product announcements to Digital Engineering.
Press releases may be sent to them via [email protected].
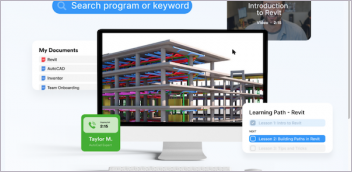

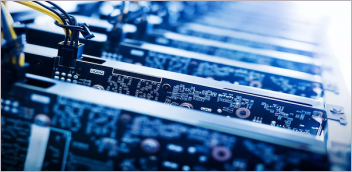
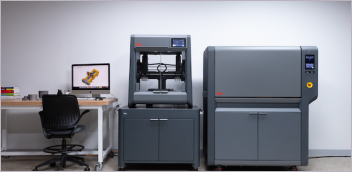