Latest News
September 8, 2011
By Jamie J. Gooch
You probably know the name Altair Engineering from the company’s popular HyperWorks enterprise simulation software, or maybe its PBS Works on-demand cloud computing technologies. But did you know the company also designs buses?
The old adage that necessity is the mother of invention certainly holds true in this case. The inspiration behind Altair’s BUSolutions program initiative was driven by its global product development consulting organization, Altair ProductDesign. Through its consulting practice in the transportation industry, it became clear to the Altair subsidiary that the business challenges faced by owners and operators required an entirely new bus development process and design. So Altair decided to create one.
The new LCO-140H bus hits the road. Designed by Altair to innovate in the
commercial bus industry, it is lighter and more fuel efficient than traditional
designs.
Thinking Out of the Box
Comprising senior management, designers, simulation experts and vehicle development engineers, Altair launched BUSolutions, an internally sponsored “stretch” program. It was designed to stretch employees’ thinking and skills into new areas. The cross-functional team sought to apply their knowledge and a simulation-driven design methodology to develop a next-generation bus design.
Of course, the BUSolutions engineers used Altair products to develop the bus from the ground up. The core design synthesis tool for the project was OptiStruct, Altair’s finite-element based technology. Part of Altair’s HyperWorks suite of CAE tools, OptiStruct helps create minimum mass concepts that meet performance and safety targets. Besides using OptiStruct, Altair engineers employed the full range of its HyperWorks tools, including solidThinking software used by industrial designers, to create conceptual designs at the beginning of the project.
![]() | ![]() |
James Scapa (left), chairman and CEO of Altair introduced the LCO-140H at the Altair headquarters in Troy, MI. Mike Heskitt (rigt), COO of Altair ProductDesign, led the LCO-140H project. |
Nothing was taken for granted when designing the new bus—from the lighting to the seating layout to the powertrain. The designers had no pre-conceived notions of what a traditional bus design had to include, so they were free to create something entirely new.
When starting from scratch, it’s not unusual for the design to evolve. The hybrid hydraulic powertrain was one such evolution.
“When we began this program, our intention was to do a low-cost-ownership, lightweight bus, but at that point did not have a hybrid planned,” said Mike Heskitt, chief operating officer at Altair ProductDesign. “Throughout the period where we began the program, the economy changed, the public awareness of hybrids changed, and the technology matured. It became evident that it made sense to put in a hybrid powertrain. The way the bus is designed, we can actually do a version that is non-hybrid toobut the hybrid is by far the better plan. It saves you money.”
The hybrid hydraulic powertrain uses technology from Parker Hannafin that is able to recover and store energy from braking. With the frequent stops a bus makes, the system helps drastically reduce fuel consumption.
Another adjustment came in the form of material choice. The company’s first choice was steel, but it turned out to be a detriment to cost savings.
The LCO-140H Bus At A Glance
|
“We designed this as a stainless steel bus, and when we went to do the demonstrator, the cost for the steel—because it was a very unusual steel—we couldn’t get anyone to roll the steel for us,” said James R. Scapa, chairman and CEO of Altair. “At first my guys were like ‘no we can’t make it out of aluminum.’ I made them do a study and the study came out fantastic.”
“Fantastic” in terms of structure and fuel economy, said Scapa. “We were projecting a 45% improvement over traditional diesel and we ended up over 100%,” he says.
According to Heskitt, that was the one aspect of the bus design that they did not predict. “We were somewhat conservative going in, so ]the fuel economy] actually exceeded our expectations,” he said. “Honestly, the major surprise was that the performance ended up much better than we hoped for.”
From Concept to Reality
Yesterday, the design hit the road. Altair ProductDesign unveiled what it called the world’s first series hydraulic hybrid transit bus. The LCO-140H (Low-Cost of Ownership-1st 40-ft. Hybrid) was developed under the BUSolutions program in partnership with Automation Alley, Michigan’s largest technology business association.
Compared to the database of buses tested at Altoona, where the Federal Transit Administration (FTA) certification program is conducted, Altair says the LCO-140H fuel economy results are 110% better than conventional diesel buses and 30% better than diesel-electric hybrid buses available today. The LCO-140 achieved an industry high fuel economy of 6.9 mpg when tested using the downtown “stop-and-go” duty cycles and test protocol established by the FTA for transit bus certification testing.
Altair ProductDesign projects that BUSolutions will lower the cost of ownership by $170,000 per bus as compared to a conventional diesel bus. With the average local transit authority operating approximately 300 buses, the savings could reduce a city’s cost of transit bus operation by approximately $50 million. When compared to an estimated $27 million increase in operational costs for a similar electric hybrid fleet, Altair says the LCO-140H could provide reduced fuel consumption and emissions while improving the fiscal performance of a regional transit authority.
A Group Effort
BUSolutions may have started as an internal Altair program, but is became a collaborative effort between public and private entities. In addition to investments by Altair and Automation Alley, BUSolutions has been funded by multiple federal and state programs including the FTA and the Michigan Economic Development Corporation (MEDC). It also has received local support by southeast Michigan congressional members, transportation industry partners, and local transit authorities SMART and the Detroit Department of Transportation (DDOT).
![]() Altair designed the LCO-140H from the ground up, including making the seats (right) lighter than traditional bus seats (left) while increasing seating capacity. |
Additionally, BUSolutions strategically partnered with regional and global manufacturers that assisted in incorporating components and technologies from the transportation sector. Program sponsors include Parker and Meritor, which contributed significant driveline systems and knowledge. Various levels of support have also been provided by PRAN, Sika Corporation, Meritor Wabco, Alcoa Wheel Products, Carrier Corporation, LADD Industries, Haldex, Shaw Development, Tenneco, USSC Group, Cummins Bridgeway, Multicolor Specialties and Williams Controls.
Altair has also worked closely with local transit authorities, SMART and DDOT, to ensure the newly designed bus platform will meet regulatory requirements and address the needs of bus drivers and riders. Altair also established the BUSolutions Advisory Board to offer insight into broader community needs, as well as perspective on actual ridership issues and public-interface ergonomics. As a result, Altair ProductDesign successfully engineered the bus to incorporate design principles that will enhance the rider experience.
What’s Next
While the LCO-140H is certainly a large proof of concept, the goal won’t be achieved until it is mass produced. Commercialization and deployment is the big challenge now.
Scapa says he hopes to secure private and public funding thanks to the lower total lifecycle costs the bus could provide to local rapid transit authorities over the long term.
In the short term, the project has demonstrated Altair’s abilities to develop vehicle plans as well as the product itself. But the company’s not prepared to hand off its 40-ft.-long baby to just any manufacturer.
“The Altair team will continue to be involved as the engineering entity for the commercial product,” says Heskitt. “We’re in this till the end.”
For more information, visit Altair BUSolutions.
Sources: Onsite interviews by Tom Conlon, publisher of DE, press materials received from the company, and additional information gleaned from the company’s website.
Subscribe to our FREE magazine,
FREE email newsletters or both!Latest News
About the Author

Jamie Gooch is the former editorial director of Digital Engineering.
Follow DE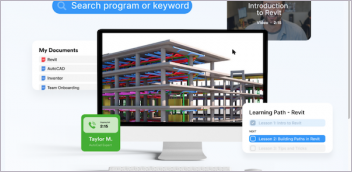

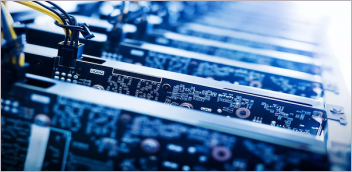
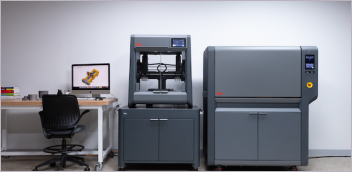