AIM3D Presents the Voxelfill Process
The Voxelfill principle overcomes inhomogeneous strength properties through a cross-layer filling strategy, according to company.
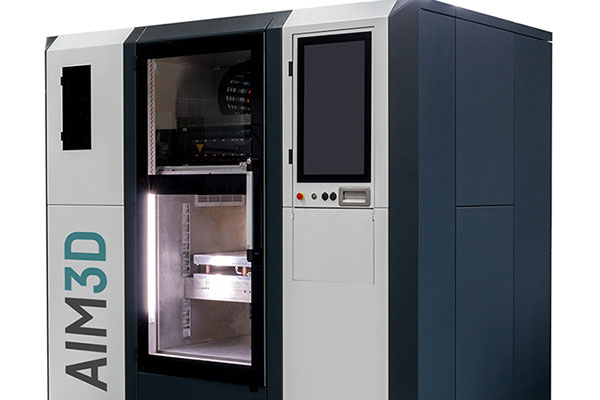
The new ExAM 510 offers a greater build area, higher precision and accelerated build speeds. Image courtesy of AIM3D.
Latest News
October 7, 2022
A common technological challenge is that layer-based 3D build processes of polymers often exhibit inhomogeneous structural properties, according to AIM3D. With its Voxelfill process, AIM3D is working to overcome inhomogeneous strength issues by achieving defined, selective densities in the component, the company reports.
At Formnext 2022 and K 2022, two fall trade fairs in 2022, AIM3D plans to provide information on two highlights. The first is the new Voxelfill process for sustainably improving the strength properties of a layer-based 3D component and second is the market launch of the ExAM 510. This system complements the ExAM 255 with a greater build area for large component volumes and will be shown in action at the trade fairs.
AIM3D processes fiber-filled components based on PA6 GF30 material. The phenomenon of inhomogeneous strength properties must be resolved in order to enable a wide applicability of 3D-printed components. By using the 3D extrusion technology of the CEM process, AIM3D has developed a Voxelfill strategy that overcomes these limitations and increases the cost effectiveness of the CEM process. Voxelfill can also be used for multi-material components and is suitable for constructing 3D components using plastics, metals and ceramics.
With the Voxelfill approach, components are no longer created exclusively in layers (i.e., 2.5D), but utilize cross-layer filling by using so-called voxels as volume areas. To do this, the component contour is first created as usual as the basic structure using one or more webs of the extruded material. A lattice pattern is created inside the component, which defines the boundaries of the volume elements to be filled, similar to cavities.
The structure of the voxels to be filled resembles the honeycomb in a beehive. The Voxelfill strategy now comprises two process stages: (1) Generation of a lattice structure: the CEM system repeats this structure up to a defined height of the volume elements, then at this point the previously created cavities (voxels) are filled by injecting thermoplastic material with the extruder. (2) Filling phase of the voxels: now the second component of this 3D printing strategy is deployed: when the volume areas are filled, this does not include filling all voxels in one plane. This would again result in a Z direction weakness directly in the “seam” plane.
By shifting the volume elements halfway up the voxel, a kind of “brick-like bond” is created in the component, resulting in the yield line being offset. This results in an increase in strength and also improves the elasticity of the components in the Z direction. The introduced volume elements reduce the printing time for fully filled components and increases the cost-effectiveness of the CEM process.
Launch of the ExAM 510
K 2022 and Formnext 2022 in the autumn of 2022 will mark the launch of AIM3D's new ExAM 510 granulate printer. The company has developed this large CEM system up to the beta phase in 1.5 years. The new ExAM 510 offers a greater build area, higher precision and accelerated build speeds. The ExAM 510 printer is a multi-material printer for additive manufacturing that can consecutively print up to three materials. The increased build area of 510 x 510 x 400 mm³ now opens up new applications. The build area can be heated up to 200 ºC to reduce the stresses in the component and to process high-performance materials. The increased build rate or print speed depends of course on the material used and can be as high as 250 cm³/h (when using a 0.4 mm nozzle).
Sources: Press materials received from the company and additional information gleaned from the company’s website.
Subscribe to our FREE magazine,
FREE email newsletters or both!Latest News
About the Author

DE’s editors contribute news and new product announcements to Digital Engineering.
Press releases may be sent to them via [email protected].
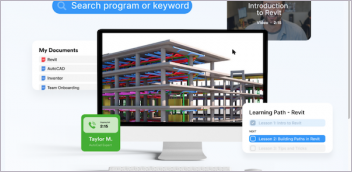

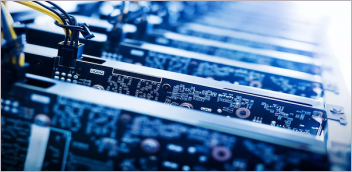
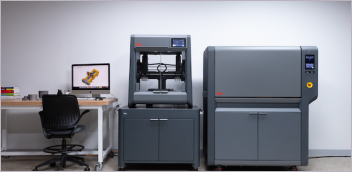