Aerospace Contract Manufacturer Reduces Cycle Time with hyperMILL
Latest News
May 23, 2018
OPEN MIND Technologies AG, a developer of CAD/ CAM software solutions worldwide, reported that its customer Concept Reality Inc. in Vancouver, WA, is increasing productivity and improving part accuracy using the hyperMILL MAXX Machining finishing module for aerospace part manufacture.
hyperMILL CAM software from OPEN MIND enables five-axis strategies for fast, easy-to-use programming, resulting in reduced cycle times and surface finishes. The integrated hyperMILL MAXX Machining finishing module, a performance package of the hyperMILL CAM software suite, is the CAM programming source enabling the use of conical barrel cutter technology to reduce cycle times over 90%. It is ideal for planar, ruled and curved surfaces often found in complex five-axis components. hyperMILL MAXX Machining offers three modules for finishing, roughing and drilling.
“On a recent aerospace project, the hyperMILL MAXX Machining finishing process allowed us to increase our step down between tool paths by 12x when compared with traditional machining methods using ball nose cutting tools. This saved us 5 hours per part in finishing operations while reducing cusp height,” says Chris Nunn, president of Concept Reality Inc.
The hyperMILL MAXX Machining finishing module makes efficient use of machine and tool options in relation to surface quality and speed, by applying an innovative five-axis tangent plane machining strategy and conical barrel cutters that use the functions of a barrel cutter and a ball mill simultaneously.
A conical barrel cutter features a very large radius ‒ ranging from 250 mm to 1,500 mm. The large radius of the conical barrel cutter makes step-over distances of 6 mm and 8 mm a reality. It does not require switching cutters in order to finish adjacent areas such as rounded interior corners, and hard-to-reach areas can be machined in a highly efficient, secure manner.
For more info, visit OPEN MIND Technologies.
Sources: Press materials received from the company.
Subscribe to our FREE magazine,
FREE email newsletters or both!Latest News
About the Author

DE’s editors contribute news and new product announcements to Digital Engineering.
Press releases may be sent to them via [email protected].
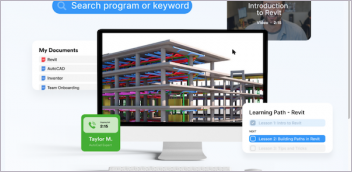

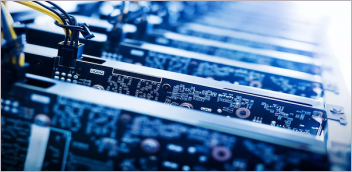
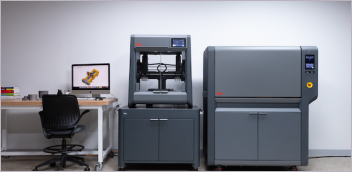