Additive Manufacturing Used to Create Heat Exchange

Webbed tube heat exchanger designed by the Clark School of Engineering and printed by Stratasys. Courtesy of Clark School.
Latest News
February 15, 2012
Much of the promise of additive manufacturing (AM) is the ability to custom create parts for specific jobs. Granted, subtractive manufacturing has been at this for years, but the investment in time, money and specialized tools required to build a single part makes standard fabrication methods less than ideal for jobs that require only a few parts be made, rather than thousands.
As more companies turn to AM to solve complex problems, we’ll continue to see innovation in fields that were dominated by traditional means of manufacturing. Such is the case with the heat exchange created through AM by the A. James Clark School of Engineering at the University of Maryland.
Working with the Petroleum Institute in Abu Dhabi, the Clark School’s Thermal Management of Photonic and Electronic Systems (TherPES) Laboratory was tasked with a method of creating a polymer heat exchanger that uses seawater to cool liquefied natural gas processing. Researchers originally looked to standard subtractive methods of part creation, but were unhappy with the potential expense.
Eventually Professor Avram Bar-Cohen and his research team turned to AM as a method of creating the heat exchange. AM offered the ability to create the complex geometry required of the heat exchange in a single manufacturing process, rather than multiple processes that would require specialized tools.
The result was the creation of the webbed tube heat exchanger (WTHX), which the researchers believe to be the first heat exchanger to be created solely through AM. The WTHX was built by Stratasys using fused deposition modeling. Testing showed the AM created polymer part was able to transfer heat, using a liquid to cool hot gas.
For the test, air was heated to 248°F (120°C) before being cooled by water that was 80.6°F (27°C) passing through the part. The total result was a transferal of nearly 65W of heat in the 500 cm³ WTHX.
The WTHX was created as a series of flat, rectangular plates with tubes running the length of the plates and separated by short webs. The tubes are designed to carry water that acts as a coolant, while air flow is maintained through the rectangular plates. The size and shape of the tubes were designed to assist pump efficiency and to minimize possible side effects of the low thermal conductivity of the polycarbonate resin.
Below you’ll find a video explaining the basics of heat exchangers.
Source: Clark School of Engineering
Subscribe to our FREE magazine,
FREE email newsletters or both!Latest News
About the Author
John NewmanJohn Newman is a Digital Engineering contributor who focuses on 3D printing. Contact him via [email protected] and read his posts on Rapid Ready Technology.
Follow DE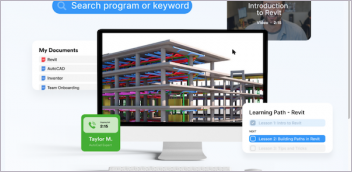

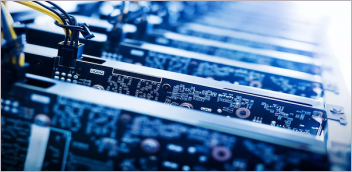
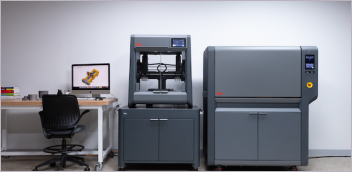