Additive Manufacturing to the Rescue for Hospital in Ethiopia

Completed sand core for a new turbine wheel, built by Voxeljet. Courtesy of Voxeljet.
Latest News
April 26, 2013
As interesting as I find the development and potential expressed by each new additive manufacturing (AM) system, I enjoy writing about humanitarian applications of the technology. AM offers the possibility of changing the world in so many different ways, such as 3D printing projects developed to help the blind better experience the world around them.
Another example of how AM can help individuals can be seen at a hospital in Walga, Ethiopia. A defective turbine wheel resulted in the hospital’s loss of electricity, and the clinic was unable to afford to purchase a replacement part. An effort to aid the hospital, led by Turbal AG, and assisted by Voxeljet, among other companies, led to the gift of a new turbine wheel.
Replacing a complex piece of machinery such as a turbine wheel can be an expensive proposition, even for well-funded organizations. Part of the problem is that subtractive manufacturing methods that have been traditionally used to build new wheels require the manual production of several sand core segments and complicated undercuts. In need of a solution to the cost quandary, Turbal AG turned to AM.
Voxeljet designed a new core that would allow the turbine wheel to be forged with a single pour. AM can eliminate many of the costs associated with the production process by generating a single core from CAD designs, rather than multiple cores that must then be assembled.
“Once we heard about the problem, we immediately decided to help,” said Dr. Ingo Ederer, CEO of Voxeljet. “Our 3D print technology is virtually predestined for cases such as these. The state-of-the-art printing equipment at our service center allows for the economical and tool-less production of high-quality sand molds and cores for metal casting based on CAD data, even for a batch size of one. Producing a sand core for the wheel is a routine undertaking for us.”
Building the new mold took five hours, compared to the weeks that might be required using traditional manufacturing methods. Not only is AM faster for this sort of manufacturing, it is also more accurate, resulting in a reduction in subsequent machining to finish a part. Voxeljet delivered the core to the Wolfensberger steel foundry, which completed the manufacturing process. The replacement turbine wheel was shipped off to Ethiopia where electricity was restored to the hospital.
“In our opinion, non-bureaucratic direct-help projects such as these are very effective and also ensure that help goes exactly where it is needed,” added Dr. Ederer. “Voxeljet was pleased to be able to make a meaningful contribution to a meaningful project.”
Below you’ll find a video about the production of the turbine wheel.
Source: Voxeljet
Subscribe to our FREE magazine,
FREE email newsletters or both!Latest News
About the Author
John NewmanJohn Newman is a Digital Engineering contributor who focuses on 3D printing. Contact him via [email protected] and read his posts on Rapid Ready Technology.
Follow DE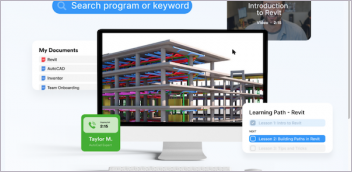

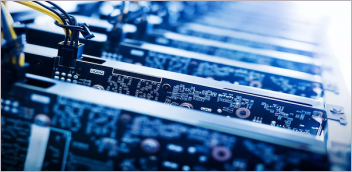
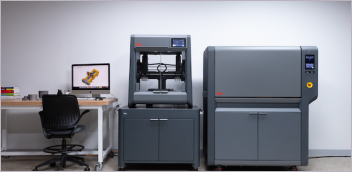