Additive Manufacturing Benefits Add Up
The beginnings, benefits and business of design-driven manufacturing.
Latest News
September 1, 2011
By Andrew Snow
It’s no surprise to any engineer that we learn by designing. Lately, what laser sintering adopters learn by design—and teach one another—is a new approach to manufacturing.
Here’s a recent example: Design consultancy firm Within Technologies partnered with 3T RPD, a prototyping and additive manufacturing firm in the UK, to explore a bold new design for a heat exchanger. Neither company was aiming for the conventional shell, tube or plate type of exchanger.
Within used its Within Enhance optimization software to generate a strong, lightweight structure of repeated sub-elements, including teardrop-shaped tubes for efficient heat dispersion. Inside the tubes were “turbolators,” a series of baffle-like struts that increased internal surface area and disrupted liquid coolant flow to maximize heat transfer.
On the outside of the tubes were self-supporting, integrated cooling fins. Each sub-element was optimized so that the final heat exchanger could be reconfigured into almost any shape required (for instance, to fit inside an irregular space under a race car hood). Overall, the final compact, scalable design was as geometrically complex as a beehive “and just as difficult to imagine manufacturing.
Cutaway model of conformal cooling channels (upper left).
Cobalt chrome dental implants. Images courtesy EOS.
3T RPD used direct metal laser sintering (DMLS) to manufacture the struts, tubes and fins all at once. The resulting structure is optimal in many ways: in weight—reduced up to 80%—in strength and in functionality.
This story is a microcosm of what designers are discovering worldwide: that rapid prototyping systems fill a market niche and, in many cases, enables the series production of designs that are too costly or time-intensive to create by traditional methods.
There is a market-wide transition occurring among what were formerly called rapid technologies, additive fabrication, 3D printing, rapid prototyping, etc. In fact, ASTM International committee F42 recently decided the term “additive manufacturing” is now a more all-encompassing term for these technologies, regardless their acronym and end use.
Growing Parts: A Growing Business
Additive manufacturing via laser sintering is inherently different from molding and subtractive processes such as cutting, drilling or grinding. It builds parts from the bottom up, working from a 3D CAD file that is divided into cross-sections. After the equipment deposits a single uniform layer of powder onto a build platform, the CAD data guides the laser to sinter the powder. The platform then lowers, and the process repeats layer-by-layer until it completes a three-dimensional part. The manufacturing sequence is automatic and can run unattended.
This process promises a number of benefits for designers:
- No tooling, minimal set-up and fixturing, and hardly any design change costs or amortization. Design tweaks have no downstream expenses attached, and can continue even during series manufacturing.
- Reduced turnaround times, particularly for low-volume series production. For example, the standard casting process for metal dental implants limits technicians to making 20 a day; DMLS can produce up to 450 patient-matched dental crowns and bridges within 24 hours.
- Substantial weight reduction. Components made with laser sintering can be lighter than their conventional counterparts.
- Nearly unlimited geometric complexity of parts. This capability enabled an unmanned aircraft manufacturer to produce all of the primary structures for advanced high-lift technologies, such as leading-edge blowing, circulation-control flaps, and airflow plenums, with the same plastic laser sintering equipment.
- Part consolidation that integrates functionality, eliminating product assembly times and secondary operations. To demonstrate the strength of its lightweight laser-sintered nylon components for aircraft, EADS built the “Airbike,” a rideable bicycle with each wheel, its bearings and the axle integrated into a single manufactured unit.
- Creation of features that are difficult in traditional processes. Toolmakers, for instance, no longer need to drill straight channels to carry off heat. Instead, they can “grow” integral, conformally cooled serpentine channels that twist or spiral as needed to give maximum cooling efficiency.
- Mass customization. The European Union-funded consortium Custom IMD is developing fully customizable dental and orthopedic implants, including a craniofacial plate made of polyetheretherketone (PEEK). Additive manufacture of these plates will be less expensive than cutting the titanium plates now in use.
In a single manufacturing process, you can create a spiral, a chain link, a hinge—virtually any shape of which you can conceive. And the part produced next to it, in the same batch, can have a completely different shape, or even be a completely different part. Those capabilities enable design-driven manufacturing: designs that embody pure functionality, with no compromises because of manufacturability restraints.
Building the Future
The near future offers even more promise, as laser sintering could change the way we manufacture, the business of manufacturing, and even the way we think about design.
Titanium humerus for a proposed prosthetic limb. Image courtesy DEKA.
Where is laser sintering going next? More materials, driven once again by industry demands, are in the works: metal alloys for aerospace and automotive applications, and plastics with characteristics previously not available for laser sintering. Companies that make end-products with laser sintering are beginning to explore the demanding validation and certification procedures of aerospace and medicine.
ASTM International technical committee F42 is developing standards for additive manufacturing. At press time, a sub-task team is developing process control strategies for laser sintering. It’s only a matter of time until there are military and aerospace specifications for both the materials and the process.
The Advantages Accumulate
Because laser sintering systems aren’t dedicated to building a single item, and are scalable across many industries, manufacturing can switch instantly from one product line to another, driven by market demand. They also offer more rapid production than other methods, shortening time-to-market.
Laser sintering can provide strategic advantages as well. In place of centralized, “big smokestack” manufacturing, companies can localize their production and reduce their shipping and logistics for laser-sintered parts.
The new technology can even benefit more traditional manufacturing: Companies can mitigate the risk of new high-volume product lines by gradually scaling them up, batch-producing laser-sintered initial versions inexpensively instead of investing upfront in machining, hard tooling, injection molding and other costly, high-production equipment.
But the primary business benefit of laser sintering may come from the design freedom it provides. Mass customization can be used to enable input for personalized products that turn customers into stakeholders. Because laser sintering isn’t bound to any single design by fixturing or tooling, it provides continuous opportunities for innovation, rather than having to wait for the next scheduled generation of a product. In the same way, it levels the playing field for small companies to compete with large ones without constant re-investment in equipment.
Finally, as those who already manufacture with laser sintering can testify, it brings design imagination to life, in every shape possible.
For More Information:
Andrew Snow is regional director, sales, at EOS of North America.
Subscribe to our FREE magazine,
FREE email newsletters or both!Latest News
About the Author

DE’s editors contribute news and new product announcements to Digital Engineering.
Press releases may be sent to them via [email protected].
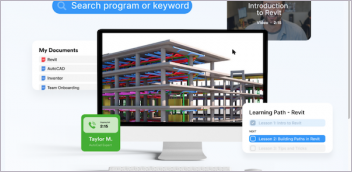

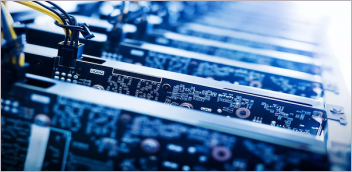
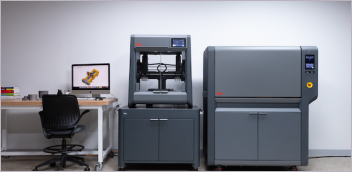