A New Look at Subtractive Prototyping, Part 2
When deciding how to invest in subtractive rapid prototyping, take these five factors into consideration.
Rapid Prototyping and Manufacturing Services News
Rapid Prototyping and Manufacturing Services Resources


Latest News
October 1, 2013
![]() Roland DGA Corp.’s MDX-540 Benchtop Milling Machine. |
It should come as no surprise that additive manufacturing (AM), aka 3D printing, has received an amazing amount of media coverage recently, literally doubling in the past year, according to industry consultant Terry Wohlers. Though 3D printing technology is almost 30 years old, more affordable options, ease of use and improved quality have recently combined to create the groundswell of interest.
But AM’s rise to fame doesn’t leave traditional subtractive rapid prototyping (SRP) out in the cold. In fact, the increased interest in turning digital designs into physical prototypes and end-use products has buoyed SRP manufacturers as well.
A Rising Tide
“As designing for 3D manufacturing devices has become more popular, more people are learning the process,” says Rachel Hammer, product manager for Rotary Devices at Roland DGA Corp. “With the additive processes out there, people are finding it to be something easy to grasp. In turn, that has helped all of additive and subtractive rapid prototyping. It’s taking it out of machine shops and into offices and making it part of peoples’ everyday lives.”
Roland manufactures and markets computer numerical control (CNC) benchtop milling machines—from the iModela Mini Milling Machine and the MDX-15 and MDX-20 Portable Scanning & Milling Machines for the hobby market, to the MDX40-A Benchtop Milling Machine, targeted to engineers who need to create prototypes, up to the MDX-540 Benchtop Milling Machines, which are used for prototyping and short runs of end-use parts. It also has machines for specialized industries, such as the dental and jewelry industries.
“We position our products as a companion to additive manufacturing,” Hammer says. “Where additive is lacking in some spaces, we can help out with that. Some customers use AM for basic prototypes and then move to milling when finalizing their project. When they actually go to manufacture it on large scale, it’ll likely be a mill creating it. Creating a part for milling in the design stage saves so much time that SRP is widely used.”
Andrew Grevstad, applications engineer for Tormach LLC, agrees that engineers don’t have to choose between additive and subtractive prototyping technologies. Tormach offers a line of personal CNC machines—the PCNC 1100 Mill and the smaller PCNC 770 Mill—and tooling equipment that are aimed at prototyping, R&D, and product development applications.
“I think it really boils own to what are you trying to accomplish with your prototyping,” he says. “Do you just want to see how it looks? If so, additive can be a good choice. If you’re looking for functional prototypes—things you’d use to do additional mechanical testing or you need a specific material—SRP is often still the only choice for that. One of cool things about machine tool technology and using it as part of your prototyping process, is at end of the day your prototypes don’t look that different than final product. You can transition to a final product quickly.”
SRP Considerations
If easy access to milled prototypes would improve your workflow, take these five factors into consideration when considering entry-level SRP equipment.
![]() Tormach LLC’s PCNC’s 770 with optional accessories. |
1. Cost vs. needs. SRP excels at producing prototypes and short-run final parts with precise tolerances. If you need that type of precision in a prototype, or the ability to quickly create a small batch of parts, then subtractive equipment is an attractive option.
The prices of milling hardware are roughly equivalent to professional 3D printers. For example, Roland’s MDX-40A retails for $7,995 and Tormach’s PCNC 770 starts at $6,850. That maps well to entry-level professional 3D printers, even with options that increase those base prices. For example: The Roland MDX-40A can be ordered with a ZSC-1 contact scanning unit ($509.99) for digitizing physical parts and an ZCL-40A Rotary Axis Unit ($3,699) for automatically positioning parts for unattended 360-degree modeling. Likewise, the Tormach PCNC 770 can be ordered with a number of options, such as a digitizing touch probe ($1,259.50), automatic tool changer ($4,200.00), a plastic injection molding attachment ($884.00), prototyping mini-lathe attachment ($1,395.00) and a 4th axis kit ($1,287.83), just to name a few.
2. Software ease of use. In the past, CNC milling required machinists to learn G-code, a programming language that controlled the machine’s toolpath and speed. While it isn’t a complicated programming language, it is still no match for the “push to print” simplicity promised by 3D printers.
Today, basic software to prepare your CAD model for SRP and control the machine is included with most benchtop milling machines, which puts G-code in the background. More intensive (and expensive) computer-aided manufacturing software is available for those who need it. See Kenneth Wong’s “A New Look at Subtractive Prototyping, Part 1” in the September issue of DE for more More Information on software choices.
3. Materials. The option to mill in many different materials is one of the strengths of SRP. Many 3D printers require materials to be purchased from the manufacturer, which can lead to higher prices. On the contrary, various metals (including aluminum), plastics, acrylic, engineered woods, plaster, styrene, and Nylon are all options for milling. However, be sure the equipment you invest in is suited to the materials you want the use. For example, the MDX-40A is not intended for metal cutting.
4. Tools. While optional features like rotary 4th-axis milling and scanning can save time and extend functionality, tools are not an option when it comes to SRP. Tools add an amazing amount of flexibility to SRP, but their cost must be weighed to make a purchasing decision. How many and what types do you need? That’s not easy to answer, says Tormach’s Grevstad.
“It really depends on what you’re trying to accomplish,” he says. “Cutting tool catalogs are a thousand pages long. There are many different ways to make the same part with a CNC approach. As far as SRP is concerned, it doesn’t have to be complicated, but you do have to identify important design features like dimensional tolerance that will dictate your approach to tooling selection—whether you choose an end mill vs. a drill vs. a reamer vs. a boring head to finish a hole, for example. Tooling is one of the things that gives CNC machining a reputation for being more complicated than it is because there are so many options.”
For SRP, as opposed to large-volume production CNC milling, the basics will suit most users. “We do offer a lot of different tools, but in the greater world of milling, that’s just the basics,” Roland’s Hammer says. “The ones on our site are enough to get you started. Our SRP Player Pro beginner software lets you enter the tools you have and it will create a plan of action for your part. To make the process even easier, our higher-end MDX-540 mill is available with an automatic tool changer, which allows unattended milling when using multiple tools.”
5. Maintenance and support. SRP equipment manufacturers are well aware they’re fighting a reputation for complexity when it comes to CNC milling. Though huge milling machines run by machinists with specialized knowledge are not the same as their smaller benchtop cousins designed for prototyping, the misconception remains. To counter that, manufacturers have developed educational services, including in-person workshops, online blogs, user forums, webinars and more resources to ensure engineers have all the help they need to succeed with SRP.
Jamie Gooch is managing editor of Desktop Engineering. Reach him via [email protected].
More Info
Subscribe to our FREE magazine,
FREE email newsletters or both!Latest News
About the Author

Jamie Gooch is the former editorial director of Digital Engineering.
Follow DE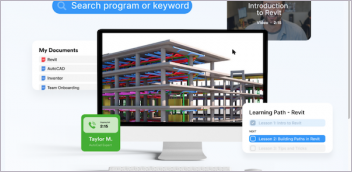

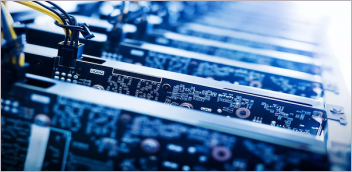
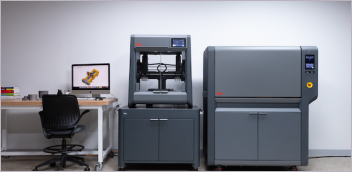