A Contemplation on Topology Optimization

The Light Rider motorcycle, the result of a partnership between Altair and APWorks (an Airbus subsidiary) has a hollow, topology optimized, 3D-printed frame that reduces weight by about 30% and allows wiring to be hidden inside the frame. Image courtesy of APWorks.
Latest News
December 1, 2016
Topology optimization is an algorithmic approach to a ubiquitous engineering problem: How can you distribute a limited resource (e.g. material), in a predefined design domain—subject to applied loads, boundary conditions and certain design restrictions—in an optimal way? In engineering terms, the state of material is discrete: at each and every spatial position material is either present or absent. Therefore, the term material distribution is often used interchangeably with terms like shape, geometry, connectivity, or layout. The word topology is derived from the Greek word topos, literally meaning place. Topology refers to the study of place, the relative positions of the constituent parts of a structure, and the manner in which these are connected, interrelated and arranged.
Topology optimization is typically studied as a sub-field of structural optimization—with automotive, aerospace and civil engineering in mind—however, topology optimization is an attempt to generalize structural optimization, encompassing and simultaneously addressing all the aspects of structural design. In 1990 the authors of the book Elements of Structural Optimization, R.T. Haftka, Z. Gürdal and M.P. Kamat, wrote that “structural optimization is still a relatively new field undergoing rapid changes in methods and focus,” and that computational cost and integration with “general-purpose software packages for structural analysis” are some major challenges. For them, “the motivation is to exploit the available limited resources in a manner that maximizes output or profit.” That is, from the authors’ point of view, the emphasis is on the optimality of the design—exploitation of resources for maximum output and profit—defined in terms of the objective and the restrictions that form a given design scenario.
A Matter of Manufacturability
More than a quarter century later, the issues highlighted by Haftka, Gürdal and Kamat have remained much the same, while structural optimization methods, and their focus, have changed. On the one hand, topology optimization methods and techniques—i.e. very detailed structural optimizations—are plagued by issues pertaining to the control of the complexity of the design: its manufacturability. If this aspect is not accounted for, a topologically optimized design may not be physically realizable, or the cost of manufacture may outweigh the efficiency and profit associated with the optimized design. On the other hand, with the development of additive manufacturing techniques, unprecedented levels of structural complexity may be realized (both in terms of the geometry and the material properties of the design). However, a human designer may not be able to the design on the level of structural complexity afforded by additive production processes. That is, topology optimization may have the potential to fully exploit the increased scope of complexity afforded by additive manufacturing techniques, and these algorithmic procedures may be the only way to translate and communicate the wishes of a human designer—an objective, and the restrictions, within a predefined design domain—to the additive production process. This automated avenue of design and manufacture—which may be the so-called third production revolution—is buttressed by a continual increase in common computational capabilities, improvements in the efficiency of computational methods and, more recently, user-friendly integration with computer aided design (CAD) platforms.
The complex, natural-looking geometries produced by topology optimization procedures almost invariably necessitate additive manufacturing processes. Some of the geometries shown here—like the Light Rider in Figure 1—are not manufacturable with traditional production processes. Advances in additive manufacturing techniques, such as modeling of residual distortions, stresses and machining requirements, have the potential to fully exploit topology optimization techniques and vice versa. Constraints that preserve the conventional manufacturability of the design take the form of a limit on local geometric variations, leading to traditional, truss-like designs.
There is, however, a trade-off between geometric optimization on the one hand, and the increased complexity and cost of manufacture on the other. Bruce Jenkins, president of Ora Research, a research and advisory services firm, advocates a system-level approach to optimization, writing in the January issue of DE that “optimization technology offers great benefit when used early in product development to optimize the functional systems,” which are, “created and refined before geometry definition begins.”
Natural Does Not Equal Optimal
The notion that a natural-looking design is necessarily an “optimal” design should be approached with utmost caution. It is fair to say that many complex geometries may invoke connotations with structures found in nature—the patterns described by fractals, for example. Natural structures, like the cauliflower shown in Figure 2, exhibit self-similar patterns of complexity on various length scales. Topology optimization may come up with natural looking designs, but this is predominantly due to the allowance of relatively detailed geometric variations. The fact that the geometries arrived at by topology optimization procedures often resemble natural structures is pertinent because it confirms the associated differential equations—the equations of elasticity, in this case—are able to capture the character of the physical laws that govern the connectivity, interrelation and arrangement of the constituent parts of the structure. Moreover, the imposition of conventional manufacturability constraints that may result in an optimal design in terms of the entire supply and manufacture chain, work by explicitly suppressing small-scale geometric variations. That is, considering a broader scope of optimization, “more optimal” designs may look “less natural.”
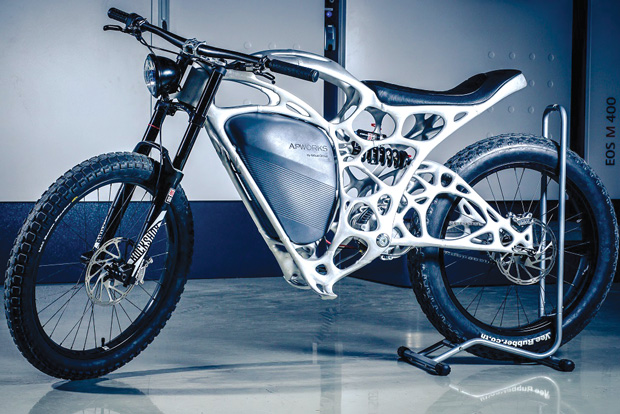
The reason topology optimization exists—and the motivation behind the pursuit of reliable and efficient methods—is its potential to produce components and structures that have improved performance characteristics and that consume resources more efficiently. In large-scale production environments, material and cost savings are paramount. In bespoke production environments, the objective often involves the performance characteristics of the design, which may include material and weight savings. Nevertheless, topology optimization is typically used after the definition of the functional systems, therefore only marginal gains may be realized in a fairly narrow design scope. Moreover, especially with recent CAD integration—software used late in most design methodologies—topology optimization may act as a translator between the designer and the manufacturing process, confining the scope for optimization.
Sustainable Progress
Taking a step back, it is perhaps prudent to keep in mind that a specialized procedure like topology optimization may inadvertently provide a semblance of sustainability to industries and resources—the automotive industry, for example, and fossil fuels—which will have to be replaced, sooner or later, with fundamentally different and unconventional alternatives. In The Beginning of Infinity: Explanations That Transform the World, David Deutsch, a quantum physicist, notes that “sustain” is an interestingly ambiguous word: on the one hand it can mean providing someone with what they need, but on the other hand it can also mean preventing something from changing.
Deutsch warns that “prevention and delaying tactics”—specialized techniques, confined to a narrow design scope, aiming at marginal, accumulative improvements—“are useful … but they can be no more than a minor part of a viable strategy for the future,” because “problems are inevitable, and sooner or later survival will depend on being able to cope when prevention and delaying tactics have failed.
“For this we need a large and vibrant research community, interested in explanation and problem-solving,” Deutsch adds. “We need the wealth to fund it, and the technological capacity to implement what it discovers.”
Undoubtedly, the marriage of topology optimization and additive manufacturing techniques will shape the machines and the structures of the future, but these algorithmic procedures should never be allowed to curb—or indeed, be purported to replace—the imaginative capacity of the design engineer.
Dirk Munro is a Ph.D. candidate under Professor A.A. Groenwold at Stellenbosch University’s Department of Mechanical and Mechatronic Engineering in South Africa. This article is an edited excerpt from his dissertation: “A direct approach to structural topology design.” Contact Munro via [email protected].
Subscribe to our FREE magazine,
FREE email newsletters or both!Latest News
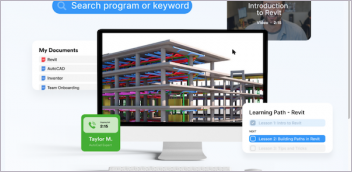

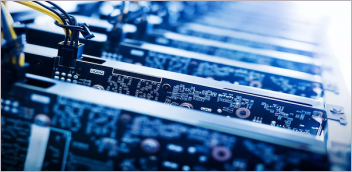
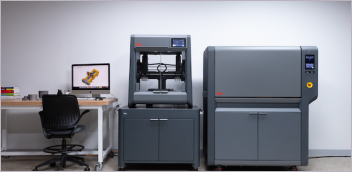