4D Printing Space Applications Lift Off
Partners Zortrax and ESA successfully create a trio of 4D printing demonstrators that print structures made of shape memory polymers and electrically conductive materials.

4D printing on display with electrically activated rotating, bending, and unfolding motion demonstrators made by Zortrax. Image Courtesy of Zortrax
Latest News
June 16, 2023
In a sign of what the fourth dimension of additive manufacturing might look like moving forward, Zortrax, a manufacturer of 3D printers, just wrapped up a research initiative with the European Space Agency (ESA) showcasing 4D printing’s potential impact on the future of space exploration.
3D printing builds physical three-dimensional objects layer-by-layer based on the digital model. In comparison, 4D printed objects have an ability to change their geometry and other critical properties in response to specific stimuli like temperature, moisture, and electric current, among other factors. The nascent technology was introduced in 2013 by MIT’s Self-Assembly Lab, a research entity at the forefront of smart materials design. The MIT group achieved the programmable shape-changing capabilities through exposure to thermal stimulus, and the goal was to mimic robotics-like behavior without the need for complex electromechanical devices like motors or actuators.
While the early 4D technology was groundbreaking, there were some problems, particularly for applicability in space exploration. Zortrax, working with the ESA, set out to resolve the challenges—among them, the fact that the early 4D printing shape shifting was triggered by a change in environmental temperature, but the entire structure needed to be heated at once. In addition, there was no way to deploy structures sequentially, which limited applications, and it wasn’t always possible to effectively control the process.
“The mostly commonly used stimulus for the activation of 4D printed mechanisms is temperature,”noted Dr. Ugo Lafont, a materials, physics and chemistry engineer at ESA. “But looking into space applications, the amplitude of temperature change can be very large and even if it can be used as a trigger for shape-changing activation, it can be difficult to control in a gradual way.”
ESA was particularly interested in 4D printing for space applications because of the potential for weight reduction of deployable structures like antennas, booms, or various sensors. As opposed to the calculation of total weight being the sum of the structure and the various deployment mechanisms, 4D printing capabilities helps eliminate the deployment mechanism part of the equation, resulting in lighter-weight objects. Through the collaboration with Zortrax, ESA set out to take advantage of thermally-induced shape-changing capabilities using a more controlled activation through heat generated by an electrical current, LaFont said.
Under the contract with ESA, Zortrax was tasked with developing three 4D printing demonstrators, each showcasing a different type of electrically-activated movement, including bending, torsion, and deployment. The Zortrax R&D team used the Zortrax M300 Dual desktop dual extrusion FDM 3D printer combined with a modified version of Z-SUITE, the company’s 3D printing software, to 3D print structures made of shape memory polymers and electrically conductive materials.
Commercially available shape memory filaments had a glass transition temperature of up to 55 degrees Celsius, which was not sufficient for space applications. To address limitations, Zortrax developed a custom shape memory filament with glass transition temperature 50% higher than anything currently available on the market. At the same time, they were able to tap off-the-shelf conductive materials to heat the shape memory polymer in the 4D printed mechanisms.
The experimental version of the Z-SUITE platform enabled bi-material printing of both materials, and the dual extrusion capabilities of the M300 Dual 3D printer enabled operation of two printing heads simultaneously.
“Combining such advanced materials in a dual extrusion 3D printing process on the M300 Dual opens a clear path towards building reliable, lightweight mechanisms that can function without separate actuators, engines, or control circuits, which is critically important in fields such as energy production, smart sensors, and defense industry,” said David Piastowski, materials development leader at Zortrax.
For a peak at Zortrax’s 4D demonstrator capabilities, check out this video.
Subscribe to our FREE magazine,
FREE email newsletters or both!Latest News
About the Author

Beth Stackpole is a contributing editor to Digital Engineering. Send e-mail about this article to [email protected].
Follow DE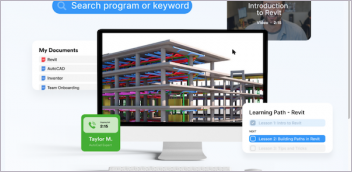

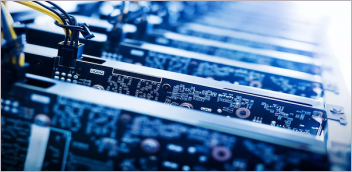
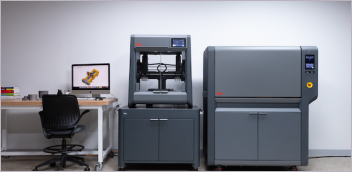