3DS/Bastech Offer Additive Manufacturing Seminars

Latest News
August 4, 2015
It’s easy to assume everyone in manufacturing is at least generally familiar with additive manufacturing (AM) and its capabilities. This often proves not to be true. It’s entirely possible for most workshops to continue operations in the same manner as it has for the last 30 years, if those involved haven’t made it a priority to keep up with technological innovations.
3D Systems (3DS) and Bastech have organized a series of AM seminars to offer a general overview of what the technology is and is not capable of producing or helping to produce. Following the 3D printing overview, the presenters also give a quick, practical demonstration of a white light scanner, and offered to discuss specific concerns with attendees.
The presentation consisted of a number of interrelated categories that allowed for a cohesive introduction to AM, along with a smattering of case studies to highlight specific applications developed by a variety of companies, including Citizen Watch, GM and GE.
Starting with the earliest stages of design, AM can help speed up and simplify the design process. Rapid prototyping offers engineers and design teams the opportunity to fail often and fail early. Problems that might not be easily detected by looking at a 3D or 2D design can be sorted out more quickly looking at a prototype that can be produced in a few hours, or overnight at the latest.
Once a part or product has been completed, prototypes can also act as sales models. Using an actual, physical model gives customers a chance to touch the product, connecting them to it in a more meaningful fashion. If a prototype is designed and printed specifically to be used as a sales tool, it can be built color coded to draw attention to specific parts of the model, or allow for easier identification of important areas.

According to the presentation, Citizen Watch initially used AM solely for the purposes of initial design prototyping, and was content to send its orders out to service bureaus. In-house suggestions for the development of custom tools to help speed up manufacturing led to the company eventually purchasing its own AM system. The purchase paid for itself in six months by reducing manufacturing costs and improving production times.
Although the majority of prototypes are non-functional, it is possible to create prototypes with enough durability to ensure a design works as intended. GM used rapid prototyping in nearly every stage of the design process when working on the new Malibu, and it resulted in time and production cost savings. Companies have even been able to build functional engine prototypes using AM, which act as proof of concept.
While it often appears as though AM and older, traditional forms of subtractive manufacturing are competing against each other, this isn’t always the case. AM can provide services to maintain and improve traditional manufacturing. One example of this is rapid tooling.
One example of how the two type of manufacturing can be complementary is that of a mold built using AM. The mold was designed over the course of a few days, printed in six hours, and put to work the same week. Although it was created using AM, the mold still showed no signs of wear after 100 pieces were stamped.

Use of AM to build tools can also provide a greater degree of design freedom than tools built using traditional methods. It is possible to create nearly any geometry with AM, and it is also possible to build highly complex tools in one piece, rather than several pieces that require additional assembly before they can be put in production.
The presentation listed functional prototypes and end-use 3D printing as two separate areas, but in either case you are using a part or product that has come directly off an AM system. Generally, reduction of material waste is one of the largest advantages to using AM to build a part, particularly in cases where the material of choice is highly expensive.
End-use parts printed on demand can also reduce the amount of warehouse space required. Instead of keeping one or more of each part on hand, companies can keep a digital inventory of parts and print new ones out as necessary.
The seminar seemed highly informative to the audience I was a part of, which seemed to consist of people without much working knowledge of AM. If you, or part of your team, are interested in seeing what AM can offer for your company, attending one of the remaining seminars, or a similar introductory event, can be eye opening.
Below you’ll find an overview of the HandySCAN 700.
Subscribe to our FREE magazine,
FREE email newsletters or both!Latest News
About the Author
John NewmanJohn Newman is a Digital Engineering contributor who focuses on 3D printing. Contact him via [email protected] and read his posts on Rapid Ready Technology.
Follow DE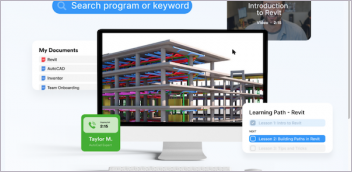

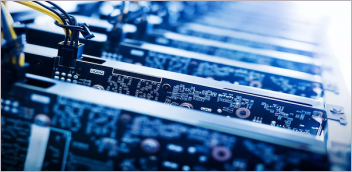
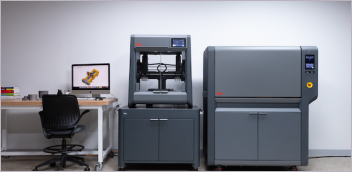