3D Printing’s Next Frontier
Latest News
May 2, 2016
If you follow the 3D printing market in the mainstream media, it may look like it’s cooling down. 3D Systems discontinued its consumer-focused Cube 3D printer. Solidoodle, once and up-and-coming manufacturer of consumer 3D printers, has ceased operations. And last year 3D printing went from making headlines for new startups to making headlines for stock market declines. But that’s only part of the story.
According to Wohlers Report 2016, the additive manufacturing (AM) industry, consisting of all additive manufacturing products and services worldwide, grew 25.9% (CAGR) to $5.165 billion in 2015. The CAGR for the previous three years was 33.8%. The firm reports that despite challenges, growth continued in many segments of the diverse industry, particularly in metal AM and the desktop 3D printer segments. In 2015, 62 manufacturers sold industrial-grade AM systems (those valued at more than $5,000), compared to 49 in 2014, and twice as many as the 31 companies that sold industrial systems in 2011.
So while consumer 3D printing hype may have plateaued for now, the 3D printing industry as a whole is still growing at an impressive rate thanks in part to industrial investments. At the Inside 3D Printing Conference last month in New York, Terry Wohlers said even most of the sub-$5,000 3D printers were sold to industrial users, not consumers. Given the amazing success the dental and medical sectors are seeing with their adoption of 3D printing, it’s no wonder other industries are following in their footsteps. The path to industrial 3D printing is being paved by 3D printing materials and more advanced 3D printing software.
Materials Moving Forward
Not long ago, materials were a significant question mark that gave many industrial users pause when considering 3D printing. Are the materials we need capable of being 3D printed? Are 3D printed materials strong/flexible/chemical-resistant/flame-retardant enough? Is there enough supply?
Those questions have been answered to the affirmative for many industries. For example, Wohlers said Airbus is on track to print 30 tons of metal monthly by the end of 2018.
An impressive amount of research and development has gone into 3D printing materials—from composites to ceramics to 3D printing multiple materials at the same time—and it is already paying off.
Software Playing Catch Up
“Software isn’t keeping up with the technology,” said Hod Lopson, professor of engineering at Columbia University and a co-author of the book “Fabricated: The New World of 3D Printing.” Lopson was addressing journalists at a recent Stratasys launch event for the company’s new J750 3D printer. “These printers now can make so much more than the software allows us to access.
“The CAD companies, I think, need to do more to keep up with the technology,” Lopson continued. “There’s a big, big gap, and in fact I think software is holding us up from exploring the true potential of the [3D printing] technology right now.”
Where there’s a technology gap, there’s an opportunity. Will it be filled by traditional CAD software companies, 3D printer manufacturers, industry titans or startups? Perhaps it will be a combination.
Through its Spark Investment Fund, Autodesk has invested in Optomec, an additive manufacturing provider. The companies intend to corroboratively develop software tools using Autodesk’s open source Spark 3D printing platform to better connect hardware and software for additive manufacturing, according to the press release. GE Ventures has also invested in Optomec to advance 3D printed sensors, electronics and metal applications.
3D Systems and Stratasys—known primarily as leading 3D printer hardware makers—have both acquired design software companies. 3D Systems acquired Geomagic in 2013 and Stratasys acquired GrabCAD in 2014.
But 3D printers are capable of building complex parts with cores of intricate lattice structures that no human designer is going to manually push and pull their way to in any 3D CAD application. The cutting edge of 3D printing lies in software’s ability to suggest optimized structures based on engineering requirements and materials.
Advances in materials and software are the next frontier of 3D printing. Rather than slowing down, the technology is getting real for more and more industries as the return on investment is proven, the materials are formulated and easy to use, powerful software is being developed.
Subscribe to our FREE magazine,
FREE email newsletters or both!Latest News
About the Author

Jamie Gooch is the former editorial director of Digital Engineering.
Follow DE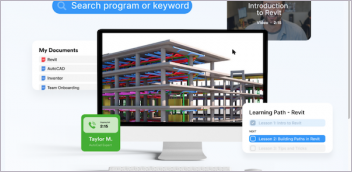

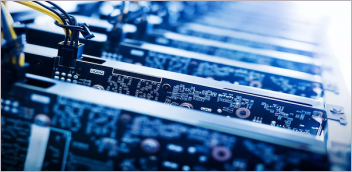
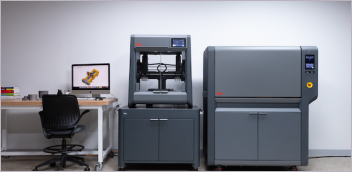