3D Printing: The new Normal for Custom Earphone Maker

Normal operates 10 Stratasys Fortus 250mc 3D printers as part of its mass customization manufacturing operation. Image Courtesy of Normal
Latest News
February 17, 2015
Earphones — our connection to the world of digital entertainment—have become an ingrained fixture whether someone is passing time on the commuter rail, hitting the ski slopes or rocking out in the back seat of a car.
But as ubiquitous as ear buds have become, it's just as common to hear bitter complaints about the gear — how they don't fit right or that they're uncomfortable. Nikki Kaufman, founder and CEO of Normal, certainly shared that annoyance. “As an athlete, commuter and music streamer, I was frustrated by poor-quality earphones that didn't fit properly, and began looking into a custom solution,” explains Kaufman, one of the founding team members of Quirky, a consumer product design company.
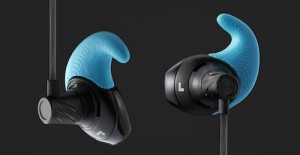
At Quirky, Kaufman was exposed to advances in 3D printing and realized there had to be a way to leverage that technology to create custom earphones at a more accessible price and process. The usual drill was time consuming and expensive. Interested parties have to visit a doctor, get silicone molds made and wait weeks before receiving their expensive, one-off product.
That is not the case with Normal, which leverages additive manufacturing technology for large-scale customization of earphones. With 3D printing at the heart of its business model, Normal is a prime example of what's to come in the new era of localized, distributed manufacturing — a transformation called out by President Obama in his 2013 State of the Union address when he said 3D printing has the potential to revolutionize how we make everything.
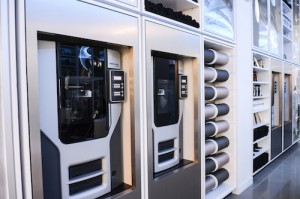
At Normal's flagship headquarters in New York City, 10 Stratasys Fortus 250mc 3D printers crank out the custom parts for the earphones using Fused Deposition Modeling (FDM) technology. Each 3D printed part of the earphone is made with ABSplus thermoplastic and is available in seven custom colors. “3D printing is imperative to our business model,” she says. “It enables us to make a custom-fit product on a mass scale at a competitive price point, and allows us to deliver it to the customer in as little as 48 hours.”
Consumers either order the $199 headphones through a free mobile app or directly from the store, and photos are collected to serve as a starting point for the custom design. Each earphone is tailored to fit the individual user's ears (the company requires one pic taken with a quarter to help with sizing) and assembled to reflect their customization choices so no two pairs of Normals are identical. Often, there are even variances between the individual buds in a pair, Kaufman says. “Our philosophy at Normal is that 'one size fits none' — everyone's ears are different and we want to build products that meet those needs.”
Having the Stratasys 3D printers at work in full view inside the Normal store sets the company apart for delivering a different kind of retail experience. “The 3D printers put the technology on display in a way never before seen and allows customers to watch Normals be printed and assembled in real time,” she says.
While Normal's focus is on custom headphones today, Kaufman says the idea of custom products being made by 3D printing is certainly not limited to headphones.
To hear Kaufman talk about the genesis of Normal and its 3D printing-centric business model, watch this video clip.
Subscribe to our FREE magazine,
FREE email newsletters or both!Latest News
About the Author

Beth Stackpole is a contributing editor to Digital Engineering. Send e-mail about this article to [email protected].
Follow DE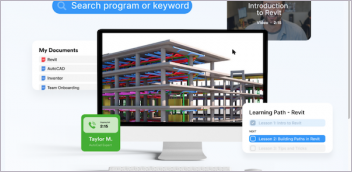

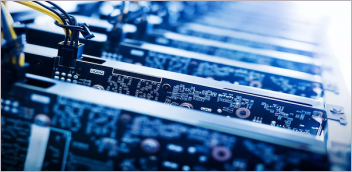
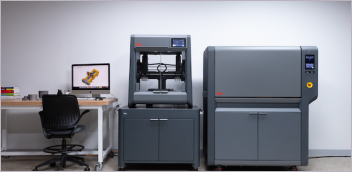