3D Printing Rescues Navy Radios

Latest News
June 15, 2016

The U.S. Navy has been tinkering with 3D printing and additive manufacturing for several years. While some of their efforts are targeted at light-weighting ships, they have also begun putting 3D printers on ships to test out the potential of producing parts and components at sea to make their vessels more self-sustaining.
According to an article in Stars and Stripes, those on-ship labs are paying off in other ways. Officers in the 3D printing lab aboard the USS Harry S. Truman have developed a special clip for handheld radios that is saving the Navy thousands of dollars.
The ship’s combat systems department was having trouble with a clasp on its handheld radios that frequently breaks. Lt. j.g. Casey Staidl and other officers came up with a figure-8 shaped solution (the Tru Clip) that has solved the problem at a fraction of the cost of replacement. Each Tru Clip costs 6 cents to produce; a single clasp replacement previously cost the Navy $615.
“It doesn’t look pretty, it’s not a real sexy innovation, but that alone has saved us a ton of money,” Staidl said. “In the past 2 ½ years, Truman has spent $146,000 just on these pigtail attachments alone.”
The ship is also sending the digital file to the International Space Station, where astronauts will print the clip using the printer on board the ISS. The first Tru Clip in space will be printed on June 17 during the White House National Week of Making.
The Truman is the first aircraft carrier with a 3D printer. There are also printers on the USS Essex and USS Kearsarge, both amphibious assault ships.
According to the article, the printer on the Harry S. Truman has also been used to fix anesthesiology hoses and to produce protective switch covers.
Source: Stars and Stripes
Subscribe to our FREE magazine,
FREE email newsletters or both!Latest News
About the Author

Brian Albright is the editorial director of Digital Engineering. Contact him at [email protected].
Follow DE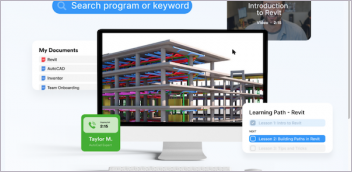

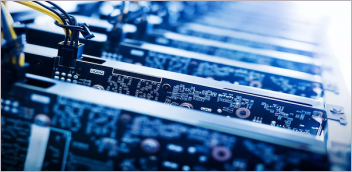
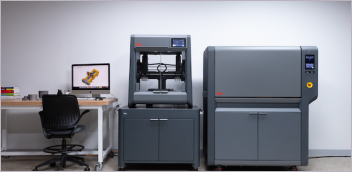