3D Printing Meets Sustainable Wood Parts
Desktop Metal launches Forust, a new AM process for producing luxury custom wood pieces.

Latest News
May 16, 2021
With 3D printing now the production engine for everything from custom prosthetics to spare parts to bespoke clothing, the question is fast becoming what can’t the technology be used to produce. Well, you can check wood parts off the list thanks to Desktop Metal’s new Forust AM process designed for the manufacturing of functional end-use wood parts.
The Forust process employs Desktop Metal’s patented single pass binder jetting AM technology to rematerialize waste byproducts from wood manufacturing (cellulose dust, for example) along with lignin from the paper industry to create isotropic, high-strength wood parts, that incorporate a natural looking digital grain.
Because the process is based on AM technologies, prospective customers in industries from manufacturing to architectural design can gain access to custom wood pieces for home décor, transportation, or other uses cases that would not be possible to produce with subtractive wood manufacturing methods, officials said. In addition, because the process makes use of waste byproducts, not actual trees, it promotes a circular technosphere and is a more sustainable means of creating wood-like offerings, they added.
“The inspiration for Forust was to begin with sawdust and end with forests,” said Andrew Jeffrey, in a press release announcing the new service. “Through advanced CAD software, proprietary materials, and Desktop Metal binder jetting mass production platforms, we can now manufacture beautiful, functional, and innovative wood products for a variety of architectural, interior, and home goods applications from upcycled wood byproducts,” Jeffrey added.
Depending on the size of the parts, Forust uses either the Shop System or a custom version of the RAM 336 3D printer, which supports prints up to two cubic meters in volume at speeds in excess of 100 liters of parts per hours. With either printer, the layers of specially treated sawdust are spread and joined by a non-toxic and biodegradable binder. Digital grain in printed on every layer, and parts can later be sanded, stained, polished, dyed, or refinished just like any traditional-manufactured wood component. “The finished products are indistinguishable from traditionally manufactured wood products found in a store,” Jeffrey said. “The additive manufacturing process literally becomes invisible.”
Subscribe to our FREE magazine,
FREE email newsletters or both!Latest News
About the Author

Beth Stackpole is a contributing editor to Digital Engineering. Send e-mail about this article to [email protected].
Follow DE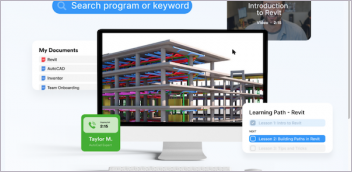

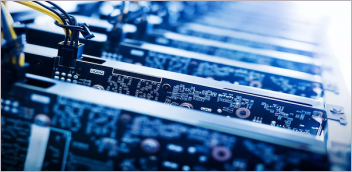
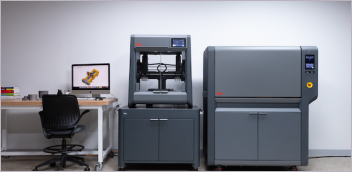