
Howard’s 3D printed prosthetic foot built using EOS DMLS. Courtesy of EOS.
Latest News
August 29, 2012
“Democratization” is a word I hear a lot of people throw around when talking about additive manufacturing (AM). What they mean by that is 3D printing offers regular people the opportunity to design something specifically for their needs. A single AM-created object doesn’t have the expenses involved with traditional manufacturing and doesn’t need to be manufactured in bulk.
We’ve covered a few examples of how 3D printing has helped individuals, but most of those efforts have come as part of a larger program or business. True democratization occurs when an individual, or, at most, a small group of people designs the solution to a specific problem and realizes a finished product completely (or mostly) on its own.
C.J. Howard was a long distance runner for the University of California. He led an athletic lifestyle before being diagnosed with osteosarcoma. The disease led to the amputation of Howard’s left leg just below the knee. Once recovered from the surgery, he returned to running and set amputee world records in several competitive events.
Later, Howard met Mandy Ott who introduced him to rock climbing. Not only did he enjoy the challenge, but he also found climbing was easier on his leg than running. The only problem was his prosthesis. Climbers rely on specialized footwear for climbing, and Howard’s artificial foot quickly wore through the shoes.
Ott, an environmental/aerospace engineer, thought about the problem and decided she could design an improved prosthetic foot, specifically for Howard’s climbing excursions.
“C.J. and I were sitting on the couch and he said, ‘It would be nice if I could have a foot that’s more suited to climbing.’ So I got out my laptop, opened an engineering CAD program, and on-the-spot created what he described, which was the shape of an aggressive climbing shoe with a downturned toe—like a banana. I just drew what he wanted. It was simple.”
To create a physical version of the CAD design, Ott turned to AM. Traditional manufacturing methods might have left seams in the prosthesis or have, “nuts and bolts sticking out” that could snag on a craggy rock face and hinder climbing. Neither of those potential problems accompanies an AM-created prosthetic.
Ott contacted service bureau Morris Technologies to print the design using an EOS (company profile) AM system and direct metal laser sintering (DMLS). Morris engineers selected commercial-grade titanium (Ti64) to build the prosthesis. Total build time for the 6 x 3 x 2 in. (152.4 x 76.2 x 50.8 mm) prosthetic foot took about 40 hours.
“Designing a prosthesis for climbing involves a little bit of trial and error,” said Howard. “Now that I’ve used this one, I know what types of climbing it works really well on and what types it doesn’t.” Ott added, “Both C.J. and I agree that there are changes that we would like to try out.”
Below you’ll find a short video demonstration of a prosthetic leg build by an EOS system.
Source: EOS
Subscribe to our FREE magazine,
FREE email newsletters or both!Latest News
About the Author
John NewmanJohn Newman is a Digital Engineering contributor who focuses on 3D printing. Contact him via [email protected] and read his posts on Rapid Ready Technology.
Follow DE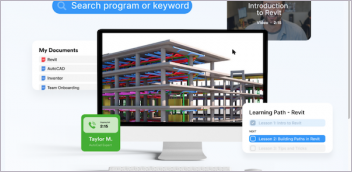

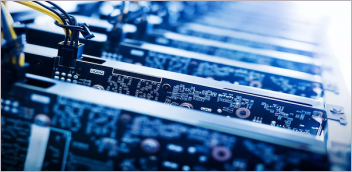
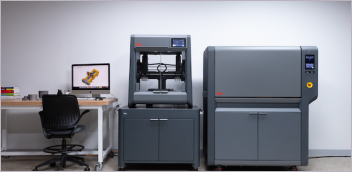