
3D printing helps bring mass ventilator to life at Óbuda University in Budapest. Image Courtesy of Óbuda University
Latest News
March 11, 2021
Just a year ago, the ventilator shortage was front-page news and a source of despair for those on the frontlines trying to saves lives as the COVID-19 virus metastasized across the globe. Today, as the virus becomes more contained, a Hungarian university has figured out a way to leverage 3D printing to jumpstart production of the first-ever mass ventilator, which can keep up to 50 patients alive at once.
After experiencing the shortages and the growing realization that the availability of ventilators was a matter of life and death, a team at Óbuda University in Budapest, Hungary, began developing a prototype for a new type of vent. The modular mass ventilator system, dubbed MassVentil, connects multiple appliances to allow hundreds of people to be ventilated simultaneously, making it ideal for extreme emergency situations.
The system works differently than a traditional ventilator. The design calls for a two-bus system: One performs overpression, ingesting air into the lung; the other has negative pressure, which aids in exfiltrating used air from a lung. Patient ventilation parameters can be adjusted for each individual patient, based on a doctor’s treatment plan.
Given the severity of the COVID-19 situation, there was pressure to create a physical prototype of the MassVentil quickly and at minimal expense. Using 3D printing technology from Craftbot, the team was able to accelerate through the prototype phase quickly and at a lower cost than planned, according to Dr. Miklós Kozlovszky, research and development engineer, and head of the MassVentil project.
Craftbot offered the team FLOW and FLOW IDEX printers to make some parts for the system, and the 3D printers ran continuously for weeks during the early production phases for the prototypes. Craftbot also provided practical advice and best practice guidance to fully leverage the FDM additive manufacturing technology for the MassVentil project.
3D printing technologies have been leveraged quite a bit to aid in providing medical equipment during the pandemic. Last year, the Federal Drug Administration (FDA) teamed up with the National Institutes of Health, the Department of Veteran Affairs, and America Makes, a national program designed to promote AM, to help hospitals and other groups output critical components closer to patients or the point of care. 3D printing was employed over the years to produce nasopharyngeal swaps for COVID-19 tests, face shields, masks and other PPE, more.
In a similar vein, a group of Johns Hopkins engineers developed a ventilator splitter device for maximizing use of limited ventilators, using 3D printing to output the design. The design includes an air-flow controller and flow meters that allow clinicians to monitor and adjust air flow for each patient. Another research collaboration between Oregon Health and Science University and Limbitless Solutions leveraged 3D printing technology to create a ventilator prototype that doesn’t require electricity in just three to eight hours.
Watch this video to learn more about the MassVentil project.
Subscribe to our FREE magazine,
FREE email newsletters or both!Latest News
About the Author

Beth Stackpole is a contributing editor to Digital Engineering. Send e-mail about this article to [email protected].
Follow DERelated Topics
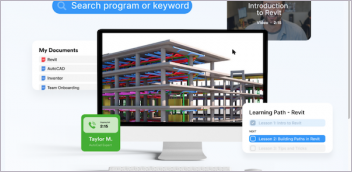

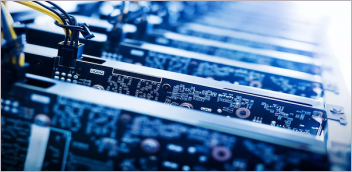
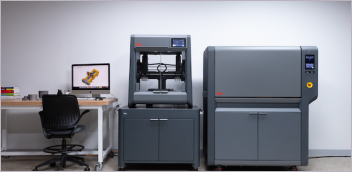