3D Printed Shelby Cobra is a Thing of Beauty

This classic appearing Shelby Cobra is actually brand new reproduction built with 3D printing. Courtesy of ORNL.
Latest News
January 14, 2015
In the future we’ll print cars. One some levels, that sounds ridiculous, but probably not to those in the know about additive manufacturing (AM). One of the big complaints about AM was that it produced parts that were too small for serious production. With the technology now boasting at least three different cars constructed primarily using AM, that time has passed.
The first serious effort at printing the body of a car was the Urbee. That program’s success inspired others, and before long we also had Local Motors’ Strati. While both of those cars were a step forward for automotive production and design, the 3D printed Shelby Cobra, produced mainly through the efforts of Oak Ridge National Laboratory (ORNL), is the most striking example of future possibilities.

The experiment began with the decision to determine how quickly it was possible to design, manufacture and assemble a car. The answer is a short six weeks. For demonstration purposes (and because it’s shiny), the team decided to base the body of the vehicle on the curves of the Shelby Cobra.
“Our goal is to demonstrate the potential of large-scale additive manufacturing as an innovative and viable manufacturing technology,” said Lonnie Love, leader of ORNL’s manufacturing systems research group. “We want to improve digital manufacturing solutions for the automotive industry.”
Rather than printing multiple parts that required additional assembly to construct the body, ORNL chose to demonstrate the power of its Big Area Additive Manufacturing (BAAM) system that it developed with Cincinnati Incorporated. (BAAM was also used for Local Motors’ Strati.) As you might expect from the name, BAAM is capable of producing larger 3D printed parts than is standard. What might not be expected is the speed with which the system works. The body of the Shelby Cobra was finished in a breezy 24 hours.
“You can print out a working vehicle in a matter of days or weeks,” Love said. “You can test it for form, fit and function. Your ability to innovate quickly has radically changed. There’s a whole industry that could be built up around rapid innovation in transportation.”
The BAAM system is basically a larger, faster version of the fused deposition modeling process familiar to most people. The initial build left behind chunky bands of strata that were far from the Shelby Cobra’s elegant lines. Part of the learning process with printing auto bodies is finishing.
TruDesign assisted ORNL by developing new methods of sanding, finishing and painting the vehicle to bring the body up to spec. That took about four hours. The final result is a car any automotive enthusiastic would be proud to own. Below you’ll find a video about the project.
Source: ORNL
Subscribe to our FREE magazine,
FREE email newsletters or both!Latest News
About the Author
John NewmanJohn Newman is a Digital Engineering contributor who focuses on 3D printing. Contact him via [email protected] and read his posts on Rapid Ready Technology.
Follow DE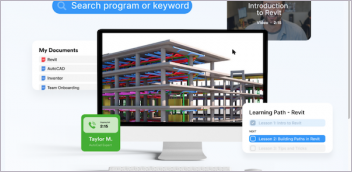

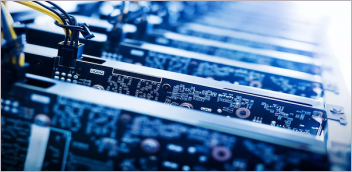
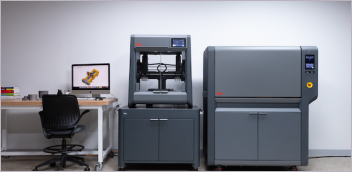