3D Metal Printing Applications on the Rise
Metal 3D printing is growing rapidly thanks to advancements in additive manufacturing technology and in materials among other advances.
Latest News
November 1, 2019
Metal 3D printing is growing rapidly thanks to advancements in additive manufacturing technology, an expansion of available materials and interest from manufacturers in shifting to the production of printed end-use parts in some applications. This is happening despite challenges around cost and quality management.
While the market is still in the early phases of adoption in many industries, interest is clearly high. According to a Markets and Markets report, the 3D metal printing market could experience a compound annual growth rate of more than 28%, reaching $2 billion by 2023.
That growth is coming from a variety of aerospace, automotive, healthcare and other applications. As this issue was going to press, a number of announcements arrived that exemplified this innovation.
The Marine Additive Manufacturing Center of Excellence (MAMCE) in Canada has partnered with the University of New Brunswick to expand and commercialize 3D metal printing. The new Design 4AM project leverages the Siemens Digital Innovation Platform and input from Sonaca for metal printing for space applications.
Printer manufacturer VELO3D and auto company PWR have partnered on a printed aluminum heat exchanger for the motorsports market. Optomec reported a 43% revenue increase in the second quarter over last year, in part because of strong demand for its metal printing products. And a number of companies are touting new technological innovations that will make metal printing faster, less expensive and more “production ready” for end users.
Exactly how this will play out over the next few years remains to be seen, but we’ve dedicated this issue to providing some guidance based on the use cases that are already emerging.
Designing for Metal Printing Processes
In this month’s issue, Senior Editor Kenneth Wong takes a deep dive into best practices for designing with additive manufacturing in mind, as well as generative design approaches that can improve results when it comes to printing metal parts.
In addition, writer Beth Stackpole presents an overview of strategies for companies that are trying to work out the economics of printing metal parts versus casting, molding and machining. I also sat down for a lengthy chat with additive manufacturing pioneer Ron Hollis (formerly of Quickparts.com, now heading up a revamped MFG) to discuss the evolution of the 3D printing market.
Outside of our 3D metal printing coverage, we also take a look this month at artificial intelligence and how it is being used for GPU-based denoising; design issues surrounding in-home robotics systems; and some advice from simulation expert Tony Abbey on analyzing shear stress for engineers.
CAASE19 Virtual Conference
Finally, thanks to all of you who participated in our inaugural Conference on Advancing Analysis & Simulation in Engineering (CAASE19) virtual event in October. We had a strong turnout and some excellent presentations from end users and experts in the simulation space.
In fact, one of our presenters, Ryobi Die Casting’s Josh Huang, focused on metal additive manufacturing in his CAASE presentation, noting how the technology can help augment and enhance existing die casting processes. He referred to additive manufacturing as a “rising star,” and praised the flexibility of design that the technology is enabling across applications.
We’ve included a rundown of some of the CAASE19 sessions in this issue (and there will be additional coverage online). If you missed the live presentation of the webinars, you can access the full conference on-demand here.
Subscribe to our FREE magazine,
FREE email newsletters or both!Latest News
About the Author

Brian Albright is the editorial director of Digital Engineering. Contact him at [email protected].
Follow DERelated Topics
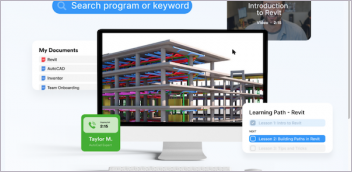

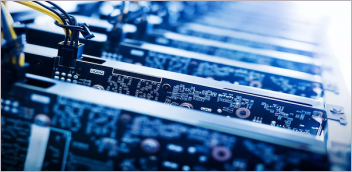
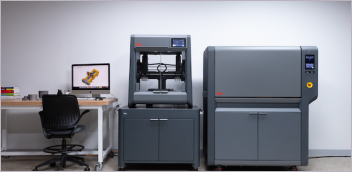