Endeavor 3D Integrates Materialise’s CO-AM with HP Tech
Endeavor 3D moved to digitally transform its processes by implementing the Materialise CO-AM Software Platform to power its 3D printers from HP.

Endeavor 3D is collaborating with Materialise and HP to onboard the Materialise CO-AM Software Platform for its HP 3D printer production capacity. Image courtesy of Endeavor 3D, Materialise and HP.
Latest News
May 3, 2024
Endeavor 3D, contract manufacturer of additive manufacturing, has announced its strategic relationship with Materialise and HP to onboard the Materialise CO-AM Software Platform to bolster its HP 3D printer production capacity.
“Endeavor 3D has a strong collaboration with HP, and integrating Materialise CO-AM enables us to offer a better experience for our customers,” says Janet Dickinson, chief operating officer at Endeavor. “CO-AM software is the right tool for us to scale our business and achieve our efficiency initiatives in 2024, which includes a 20% increase in labor productivity and a 30% yield improvement.”
In anticipation of the ongoing demand for 3D printed applications and the need to future-proof operations, Endeavor 3D moved to digitally transform its processes by implementing the Materialise CO-AM Software Platform to power its fleet of HP Multi-Jet Fusion and Metal Jet 3D Printers. By doing so, Endeavor 3D will streamline its workflow, reduce manual touchpoints and increase efficiency through automation, maximizing its production output and AM capacity.
The adoption of Materialise CO-AM software with HP 3D printers brings benefits to Endeavor 3D. Incoming requests will be stored in CO-AM’s Order Management System, ensuring organization and data storage. Team members will receive automatic notifications about status changes, enabling them to provide quicker responses to customers. When orders are ready for production, files can be launched in Materialise Magics software for data and build preparation, then nested via the Magics Nester module. This allows orders to be batched on build trays while improving Endeavor 3D’s overall production output.
The CO-AM Manufacturing Execution System manages all HP 3D printers on the shop floor, providing real-time sensor data status updates for remote monitoring and quality management. This integrated system also oversees processes such as post-processing, finishing, and quality control, ensuring workflow from production to final delivery.
“To scale additive manufacturing, the industry is in need of printers that are designed for high productivity coupled with an integrated end-to-end workflow solution that focuses on lowering the cost of additive parts in production while managing quality. The collaboration between HP and Materialise delivers this solution for Endeavor 3D,” says Arvind Rangarajan, global head of Software and Data, HP Personalization and 3D Printing. He added that a key factor driving industry growth is the willingness of industry players to collaborate and integrate with one another.
“This collaboration with Endeavor 3D and HP empowers us to drive industrial volume production with additive manufacturing,” says Udo Eberlein, vice president of software at Materialise. “The openness of the CO-AM Software Platform allows for deep integration with HP technology, which enables Endeavor 3D to optimize its production processes and build a strong foundation to scale as the company acquires more customers and expands its operations.”
Sources: Press materials received from the company and additional information gleaned from the company’s website.
More Materialise Coverage
Subscribe to our FREE magazine,
FREE email newsletters or both!Latest News
About the Author

DE’s editors contribute news and new product announcements to Digital Engineering.
Press releases may be sent to them via [email protected].
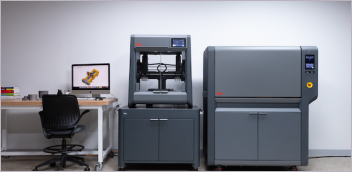
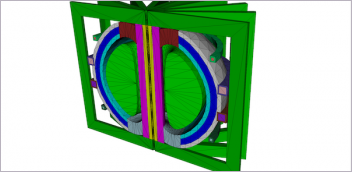
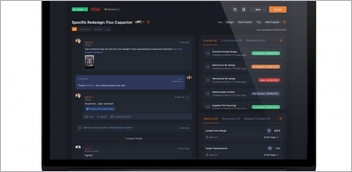
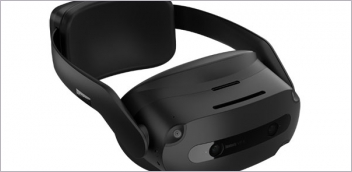